The Challenges of Affordable Reflow
The Risks of Reflow
It is easy to think that the most important part of the reflow curve is the maximum temperature of 255°C (480°F). It is difficult to build an oven that is capable of reaching those temperatures in such a short duration. However, another important number is the rate-of-rise of temperature at the higher temperatures. At those temperatures it becomes increasingly difficult to achieve the required rate-of-rise without running the heating elements at full blast. You run the risk of damaging sensitive components if the reflow takes too long, and you can create hot spots (damaged components) and cold spots (no solder reflow) if the elements glow red hot.
There are a lot of other problems that can occur if the reflow profile isn't followed. Components can be damaged from thermal shock or cracking, solder paste can splatter which can lead to voiding in array type packages, and the solder paste could oxidate or the flux not fully activate. If the maximum allowable temperature of IC's is exceeded, it can damage the internal dies of components and foster intermetallic growth leading to shortened MTBF (mean time before failure) numbers. The time-above-liquidus and cooling rate also affect the quality of the resulting solder joint.
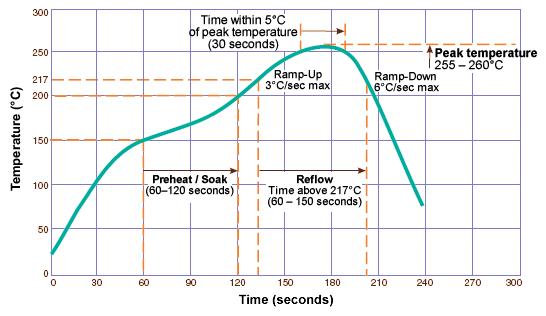
The Problematic Alternatives
Cheap Chinese Reflow Ovens (T962/T962A/T962C)
These ovens have infrared elements located directly above the boards. There are no heating elements below the boards.
- Infrared is absorbed at different rates, so expect darker components to heat up much quicker than lighter ones.
- The oven does not conform to the J-STD-020 reflow standard. Specifically, it fails to meet requirement 3.2.2: "It is required that this equipment use IR to heat only the air and not directly impinge upon the SMD Packages/ devices under test."
- All the heat comes from the top. Imagine trying to reflow a microcontroller - the black microcontroller will absorb a lot of the infrared heat while shading the PCB underneath it.
Oven with Single ON/OFF Control
You can build an oven with a single ON/OFF relay controlling power to the oven, but there are drawbacks:
- The top element is on as much as the bottom one. You cannot control heat direction.
- No control over the convection or cooling fans
- Current spikes as all the elements are turned on or off
Hot Plate
Here all the heat comes from the bottom, which is great for keeping heat away from sensitive components. Unfortunately:
- High-temperature lead-free reflow is not possible. You'll burn the PCB long before the solder reflows.
- No good automation means you need to keep a close eye on the reflow.
- How do you follow the recommended reflow profile?
The Controleo3 Advantage
The Controleo3 controller and the oven built in the build guide should be considered top-of-the-line. A lot of engineering and experience has gone into making the Controleo3 reflow oven, and there are currently more than 5000 customers world-wide using either ControLeo, ControLeo2 and the latest Controleo3.
If you are only doing small boards and using leaded solder paste you can get away with a less-capable controller and poorly insulated oven. But how much is your time worth? What is the value of the components you plan to use? What is the turn-around time to order new boards or components when they get heat-damaged? Do yourself a favor and build yourself a great reflow oven. Do it once, and do it right!